Products and Information
What is the Difference Between Flat and Tubular Webbing?
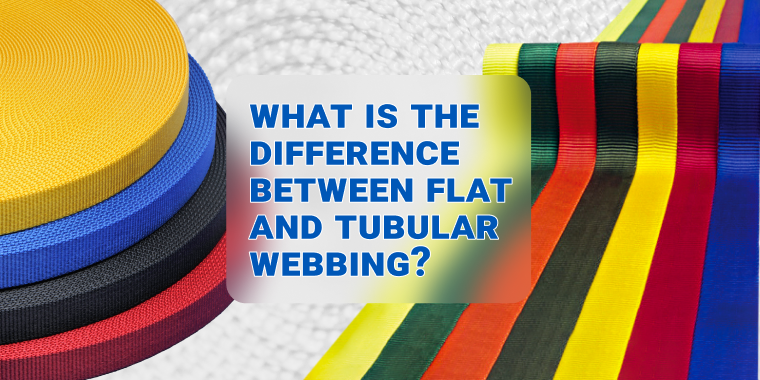
Flat Webbing
Flat webbing is thicker, stronger, and more abrasion resistant than its tubular counterpart. The increased strength of flat webbing is often preferred in harsh and abrasive environments, for use in technical rigging, and in heavy rescue situations. Since the solid flat woven construction incorporates more nylon, flat webbing weighs slightly more and can be more difficult to handle than tubular.
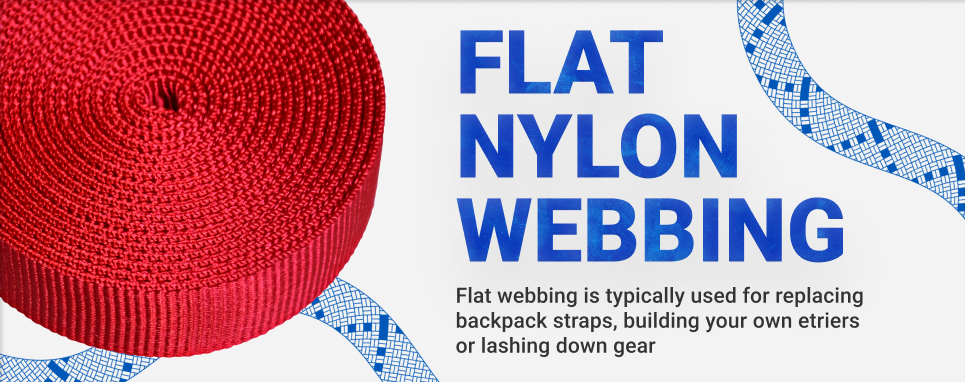
Tubular webbing
Tubular webbing is easily identified because of the hollow center, or tube-type construction. Popular among recreational sport users, tubular webbing is lightweight, strong, and easy to handle. Tubular webbing is commonly available in a wide array of colors, and is cost efficient. Tubular webbing may be constructed as Shuttle Loom or Needle Loom. These two designation refer as much to the type of machine the webbing is constructed on as to the webbing itself.
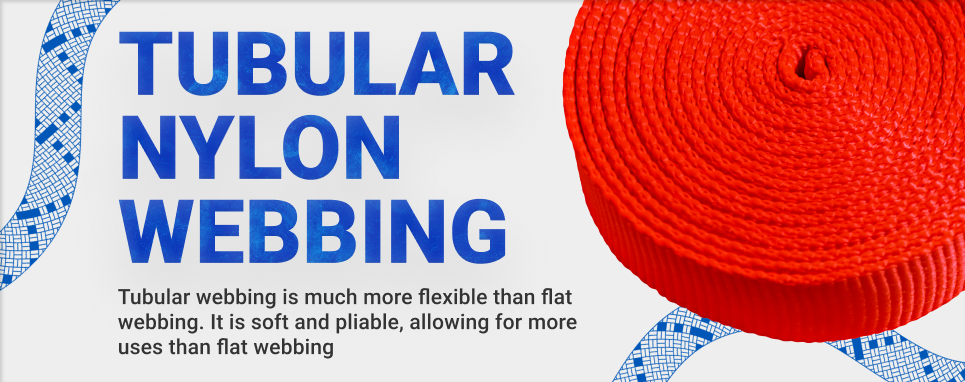
Shuttle Loom:
Historically, tubular webbing was woven to meet military specifications that designated ‘critical use’ as a Class 1, or shuttle loom construction. The spiraling weave formed a continuous tube throughout the length of nylon material. For years, only shuttle loom construction met military specifications.
Needle Loom:
As technology progressed, a Needle Loom process became more efficient and cost effective than the Shuttle Loom alternative. The early Needle Loom process constructed a flat weave of nylon that was folded and finished with a chain stitched edge to form a tube. This chain stitch was found to be unacceptable for critical use or life support, because the stitch could easily unravel.
Ultimately, improvements in equipment led to Class 1A Needle Loom webbing, which incorporates a locked stitched edge to meet the required specifications for military use. In fact, Needle Loom Webbing is now more common because of the efficiency and reliability of this newer technology.
Be aware, however, that it is possible to find 1” tubular webbing (particularly from non-life safety suppliers) that might not be lock stitched. It is always best to buy webbing from a trusted life safety product source.
All PMI tubular webbing is Class 1A Needle Loom construction and incorporates a lock stitch construction method.
0 comment